I was planning to treat myself and my son to one of those cool high-end Polaroids for Christmas but, after seeing the ZH1, I can’t think of buying anything else. This retro-looking glory is not made by Leica, Nikon, Minolta or Ricoh. It’s a camera exclusively made out of pieces of Lego. It’s built from the blocks of the most famous toy maker in the world, all the way down to its lens: A Lego magnifying glass.
In fact, the Lego ZH1 camera designer only got the idea to make it when he came across the little plastic loupe, a part that was only manufactured by the Danish toy company from 1998 to 2013. It would be perfect to design a working 35-mm film camera exclusively using Lego pieces, he thought. “I didn’t have any Lego, so I bought a few sets to begin my prototype,” Zung Hoang tells me over email. He wanted it to have a general retro look, all the way down to the logo, which was inspired by Lego’s 1934 brand. But, above all, he wanted it to be fully functional. “I initially tried using metallic parts to make it more realistic, but they easily tore off. My focus was on functionality—if a feature didn’t add any useful function, I wouldn’t include it just for aesthetics,” he describes.
This build was extremely hard to accomplish. “I began with the focal distance and added features one by one. Each function took me a few weeks to perfect,” he says.
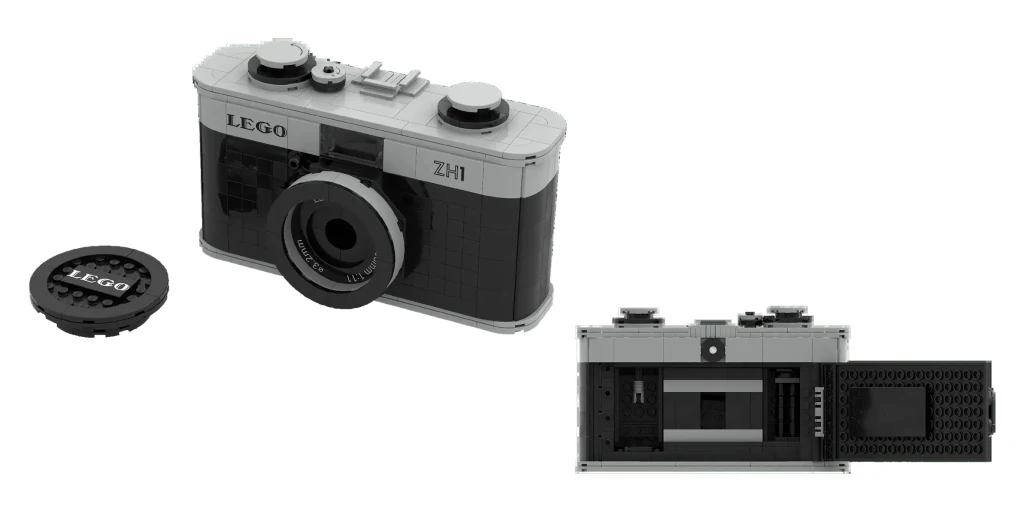
Designing a Lego camera, affordably
One of the main challenges was that he wanted to keep it as affordable as possible, which was a real struggle. The more expensive Lego sets are the ones with the most pieces, so keeping the use of piece count down to the minimum possible was a priority for submitting his project to the Lego Ideas site, the Danish company’s program to turn designs made by amateur and professional builders into actual products. After submission, fans vote for their favorite designs. With enough votes, it goes through a few phases of evaluation by Lego’s own designers until it reaches approved status. Get a sweet price spot is an important part of this evaluation process. Once approved, the company’s designers optimize the submitted plans, making any changes they deem necessary, usually reducing the number of pieces to lower the cost, making the set sturdier to it’s more playable, or avoiding any techniques that are not considered adequate per Lego standards (such as not showing enough studs in sets or arranging pieces in “not-legal” ways).
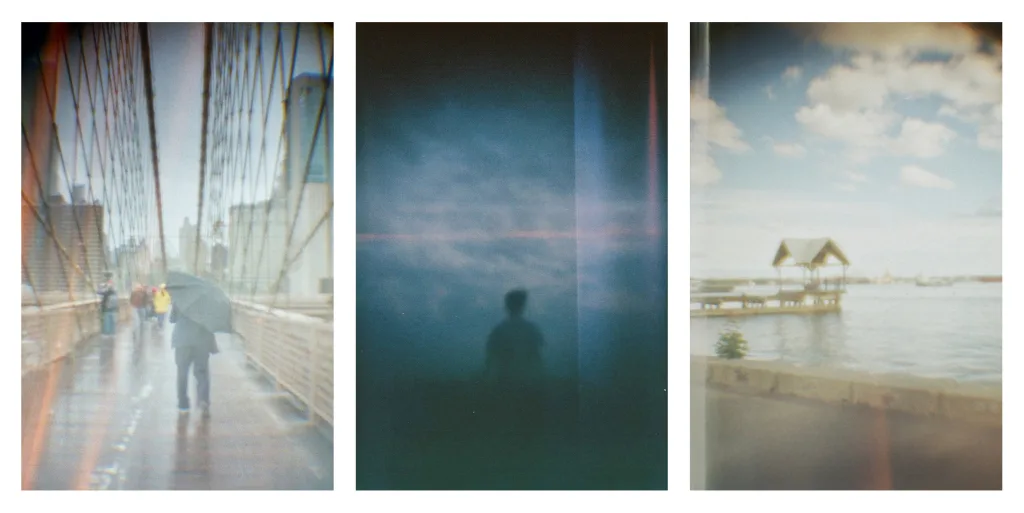
Reproducing every part needed to make a functional camera out of Lego runs against the limited parts objective, as well as the compact size he wanted. The camera needed a lot of components: Shutter button, shutter mechanism, film advance and take-up reel, wind lever with release, full-frame or half-frame modes, accessory shoe, back cover, and rewind lock mechanism. Making a working 35mm camera is even hard with modern metal machining, and Hoang discovered that recreating all those mechanisms with Lego pieces at an acceptable size was borderline impossible. Lego pieces are bigger than the tiny metal gears, axels, and springs of regular cameras. Getting each component both functional and small was a process that required him to iterate it again and again until everything worked perfectly. “The hardest part was the shutter release button. I was never fully satisfied with the results, and it took me the longest to perfect, with at least ten prototypes,” he says.
Piecing it all together
Part complexity wasn’t the only obstacle to making a compact Lego camera. The way bricks interlock introduces a big problem for photography because of the slightly flexible nature of their ABS plastic. The bricks can’t achieve perfect zero-space lock, leaving microscopic openings that let in light. And Hoang discovered that it was very hard to make a 100% lightproof body. “The early film rolls were fogged due to light leaking through bright, colorful bricks, and gaps between pieces,” he tells me. One of the first mistakes he made was using light-colored plates, which let light go through and completely burnt his first-two rolls. “Later, I switched to black plates and tried to fill the gaps using three layers [of bricks],” he says. He used a phone flashlight to identify any light leaks through the gaps until he got it perfect.
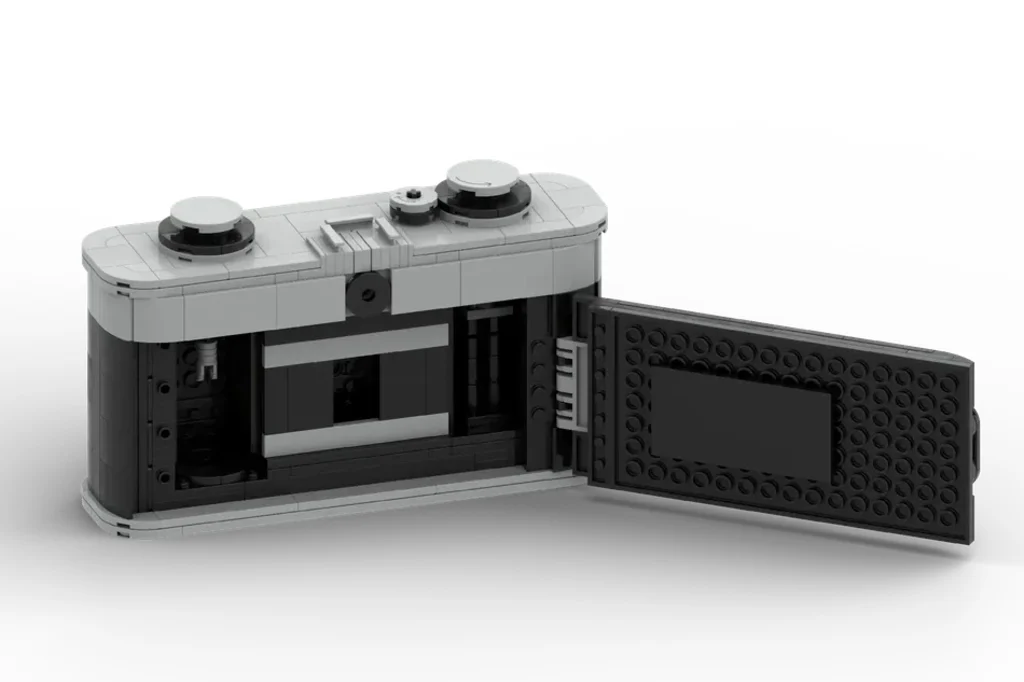
While mostly surmountable, the challenges intrinsic to Lego design meant that his dream of a truly compact 35-mm point-and-shoot wasn’t achievable. While he kept the final piece count at an acceptable 595, the final design measured a rather large 9.84 by 3.94 by 4.72 inches. Compare that to the Leica M6, which at at 5.43 x 1.57 inches x 3.03 inches., is a sizable film camera but with many dimensions measuring half those of the ZH1. The weight, however, was comparable: The ZH1 is 1.10 pounds while the M6 is heavier at 1.27 pounds because, well, it’s made out of metal, not plastic.
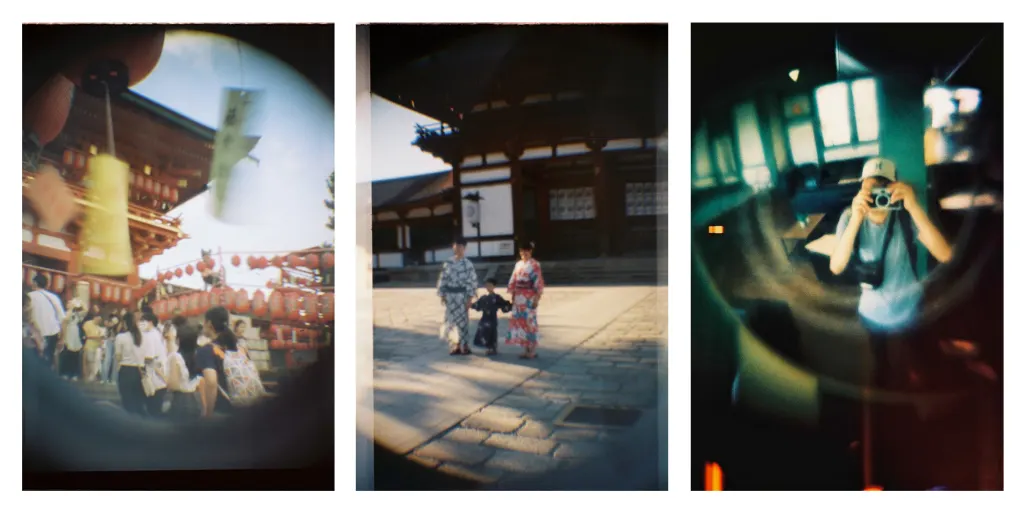
Of course, not that this size comparison matters much. The ZH1’s cool factor comes from the fact that it is made out of Lego and works, not that it takes amazing images, like the $3,000 Leica. Thanks to the imperfect, tiny plastic lens and its mechanical design, the Lego ZH1 takes photos that are quite charming and interesting, in a Lomography kind of way. The captured scenes have a soft look, with a vignette effect around them and different, seemingly random optical effects that add a touch of surreal. And given the camera’s slow shutter speed, will get lots of blur in moving objects.
If you want your own ZH1, it is not available at the Lego Shop yet. It’s still going through the selection process and you can help it succeed. If you want it, just go and vote for it right now. The world will be a better place with it. Or, at least mine will.